Machine Hammer Peening (MHP) always makes the workpiece better!
Any tool or equipment component where operating performance and life cycle improvement is desired, are candidates for peening. This includes parts subject to abrasion, wear, fatigue caused by thermal variances, fluctuating dynamic loads, stress cracking, environmental conditions, chemical corrosion, etc.
Different materials and objectives require adaptation of process parameters. These include hit rate, impact force, striker diameter & form, stroke length, pitch, feedrate, approach angle, etc. Our knowledge and experience allows us to assist you in setting up successfully for a wide range of applications.
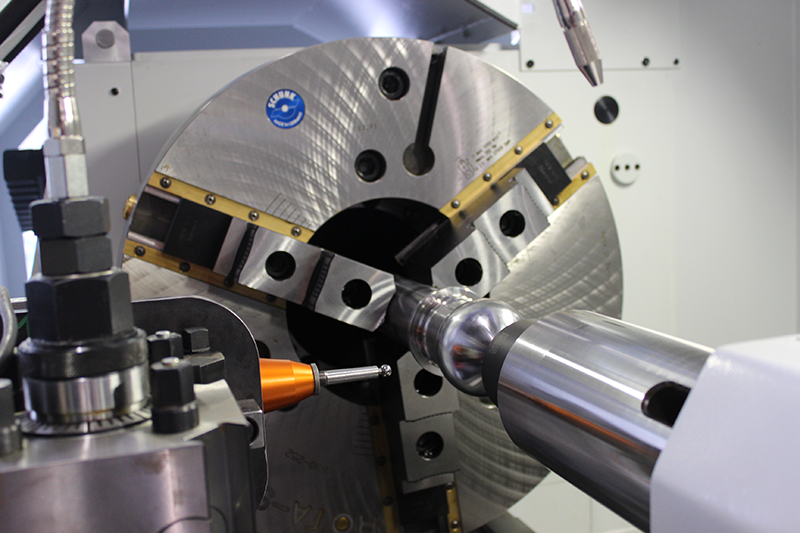
Proven results include:
Reduced friction and better material flows from improved tribological effects of sliding surfaces in contact.
Applications
Industries
Automotive
Aerospace
Oil & Gas
Petrochemical
Wind Energy
Nuclear Energy
Mining
Railway
Transportation
Forestry
Defense
Marine
Ship-building
Agriculture
Construction
Food Processing
Plastics
Medical
Recreation & Leisure